Educations
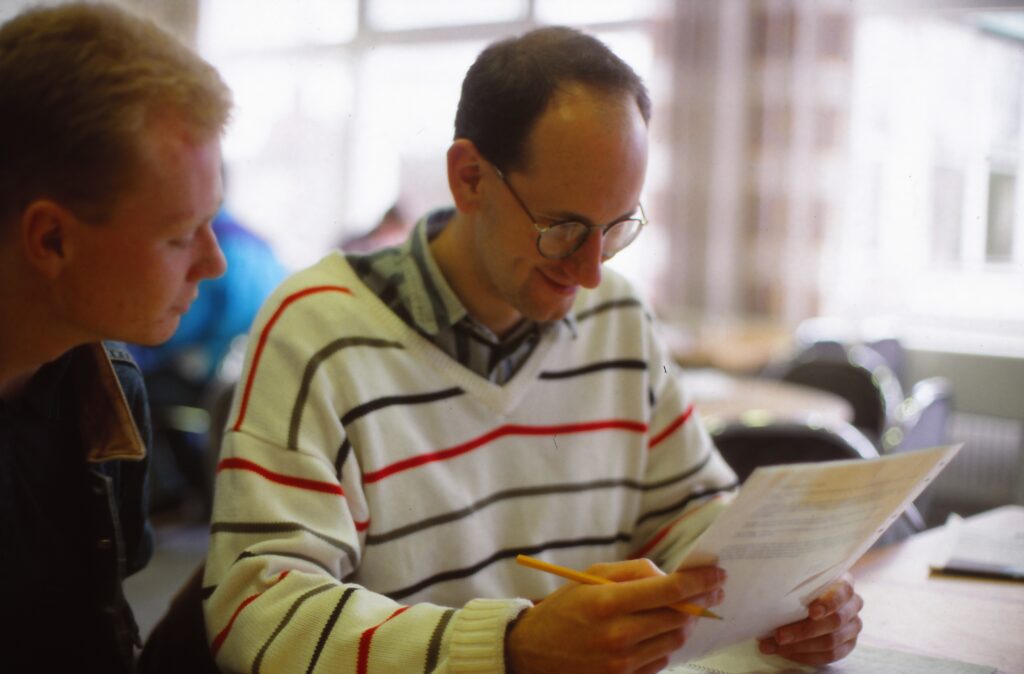
As a result of, among other things, the mature technology, and short-term profit optimization in this specific industry, it has shown that many companies have lost the technical core competence. The core technology was often developed by knowledgeable people decades ago who have long since retired. The younger ones who have been hired have rarely had the opportunity to get deep enough into the technology and often these people quit far too early, from this perspective.
As an example, very few have a deeper understanding of the torque transmission of the idling rotor and therefore they keep the current profile design, since it has worked for a long time. But with new fluids and/or gases the condition might be changed which can lead to a rattling pump/compressor and finally a possible breakdown. By having a deeper understanding this can be predicted and the profile can be optimized for the new condition.
André is one of the very few who have had the unique opportunity to learn screw machine technology in depth, as an apprentice to some of the old legends, during his many years at SRM and IMO (Colfax/Circor group). In addition, he has also had unique opportunities in the form of time to immerse himself and develop new knowledge.
It is with pleasure for us to share our knowledge through education in its many forms. In part, it can be for a group, which is usually the case for more generally educations. It can also be in the form of workshops for one or a few people, with practically exercises complemented with calculations, examples, or real problems.
The trainings are tailored based on the customer’s needs, regarding, among other things, scope, depth, group size, participants skills and available time. Below are examples of what the education may contain. We welcome suggestions for other topics that we can prepare.
Some of the sections below is relevant for all machine types (compressor, pumps, and flow meters) and some are only relevant for one or two types.
- Rotor profile design (all types)
- Rotor profile management (all types)
- Port design (compressors)
- Torque transmission from the power to the idling rotor (all types)
- Axial and radial forces (all types)
- Performance (all types)
- Cavitation (pumps)
- General pumps (pumps)
- General compressor (compressors)
- Rotor production (all types)
Education descriptions
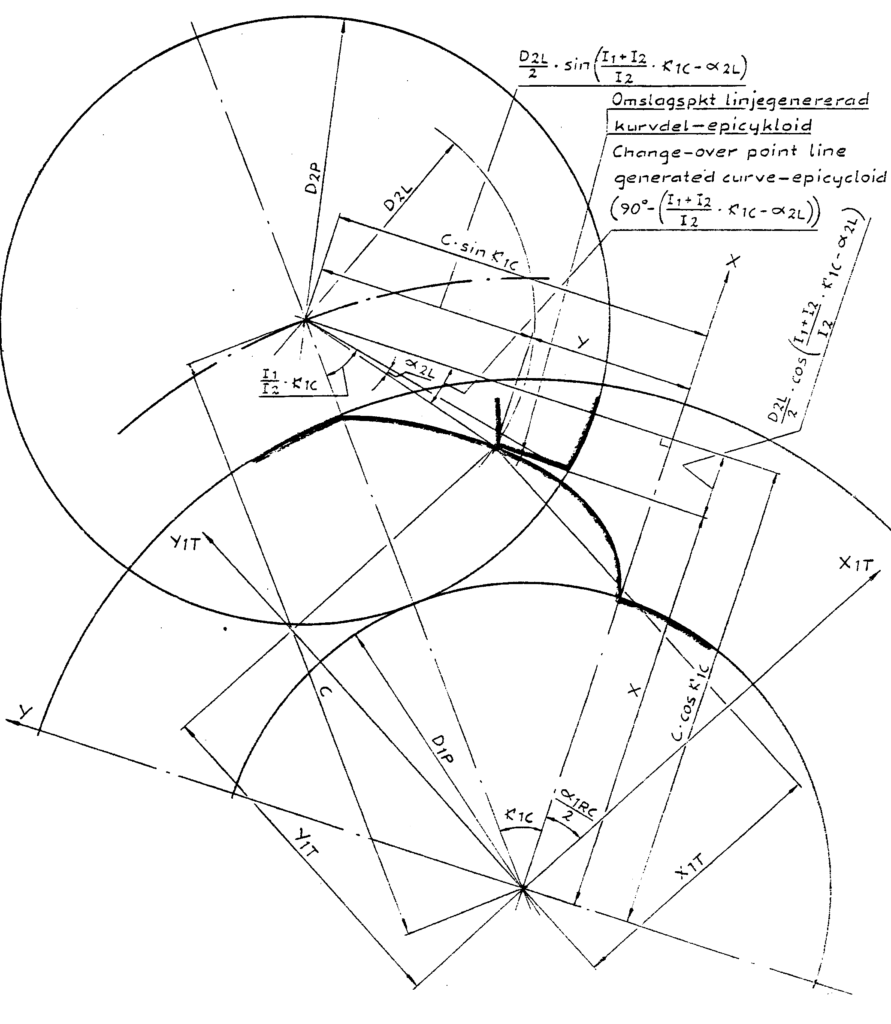
Rotor profile design
In this course section, we describe the basics of how rotor profiles are generated and the basic mathematics to give the participant a prerequisite to start design their own profiles. Depending on the chosen scope and the participants underlying knowledge, we will concretely be able to produce simpler to more complex profiles.
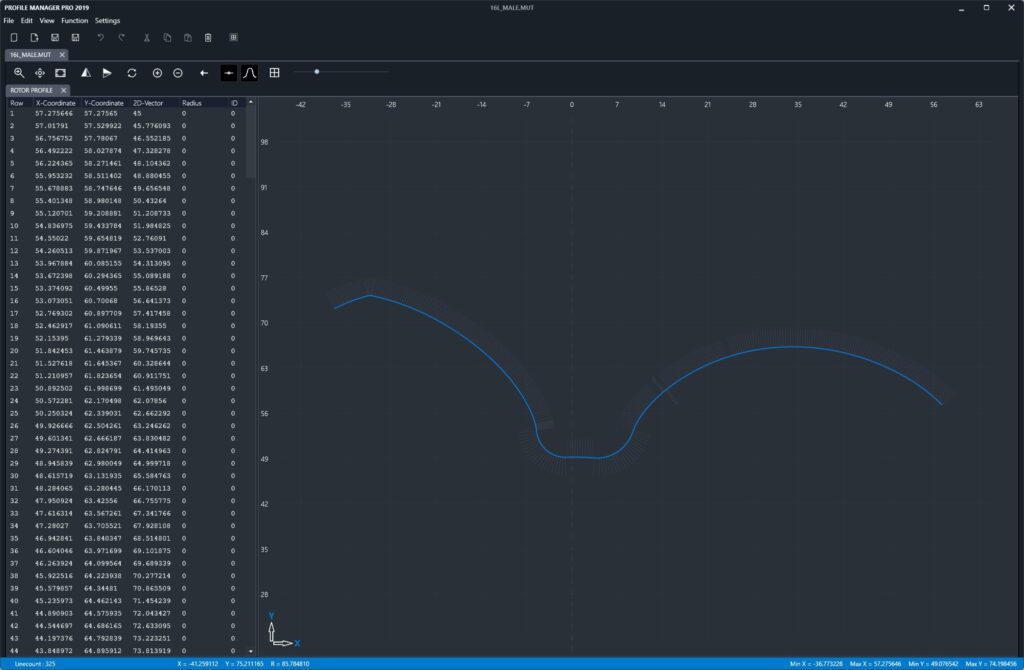
Rotor profile management
In this course section, we start from a rotor profile. We analyze it to find out if it’s production-friendly, continuously, and overall suitable for further calculations. Then we calculate the tool profile (cutter or grinding wheel) and analyze it to discover any shortcomings or practical limitations. We will go through possible problems that may arise and go through how to solve them if it’s even possible. Finally, we will go through what is required for measuring the rotors in a CMM and take a closer look at commonly occurring problems.
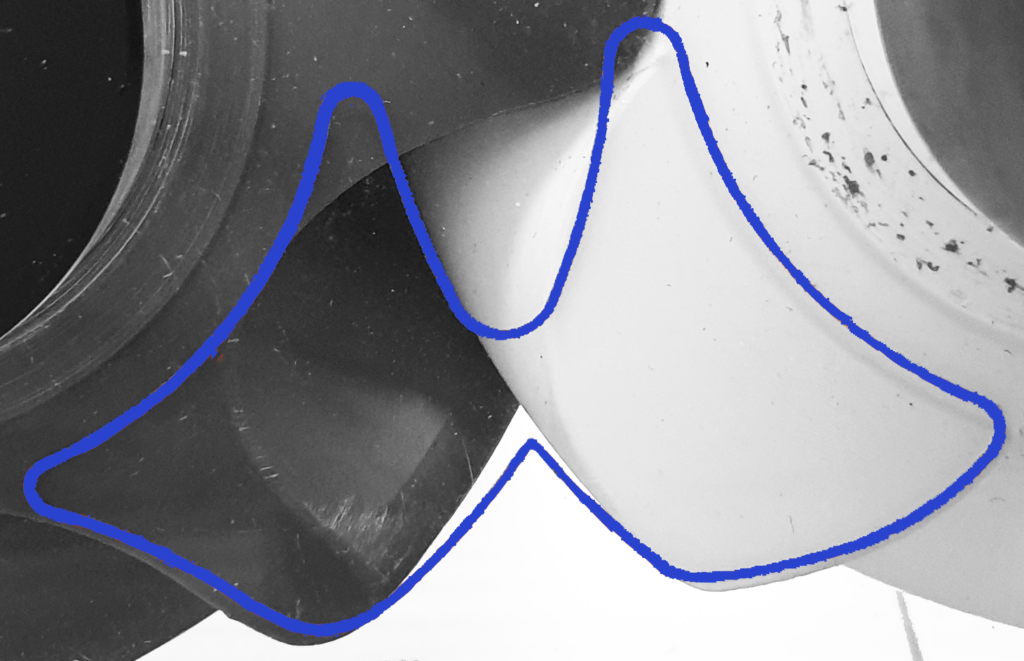
Port design
This course section describes the principle of the inlet and discharge port design in respect to required displacement and internal compression (VI), we will discuss the theoretical port and different practically used designs, to achieve cost effective production.
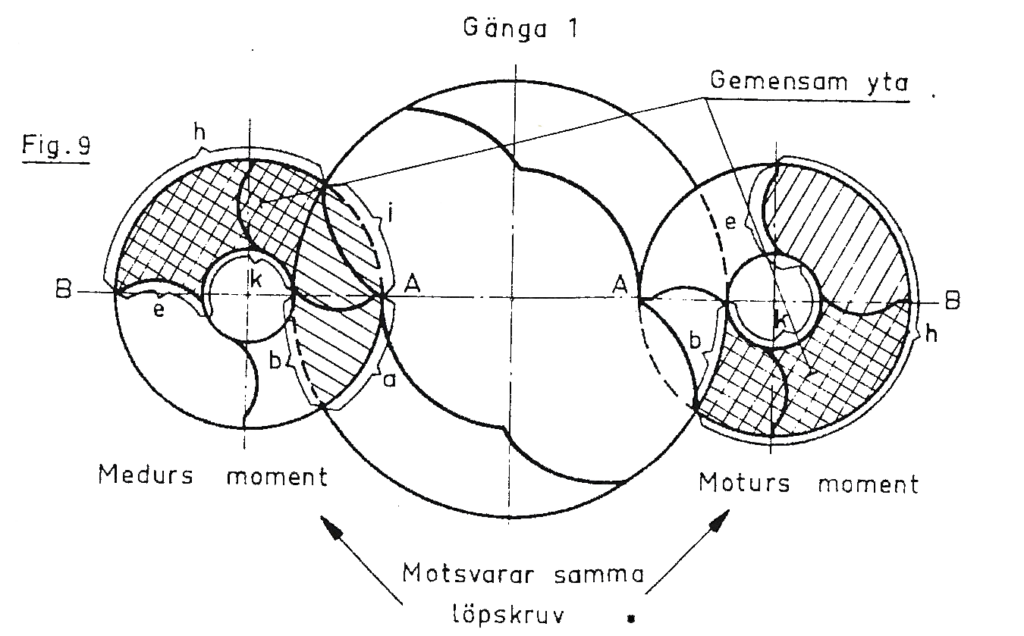
Torque transmission from the power to the idling rotor
In this section we’re, based on the sealing line, discussing how the pressure affects the rotation of the idling rotor. Most of the torque arise from the pressure, based on the profile design, the remaining mechanical transmission can become positive or negative. The remaining mechanical torque should preferrable be small, but if the torque is too small, the idling rotor can begin to alternate between being driven to drive the power rotor. In this way a rattling sound occurs, but worse is that this can lead to pump/compressor failures. It’s therefore important to have good control of the level and the direction of the remaining mechanical torque, at the factual running condition.
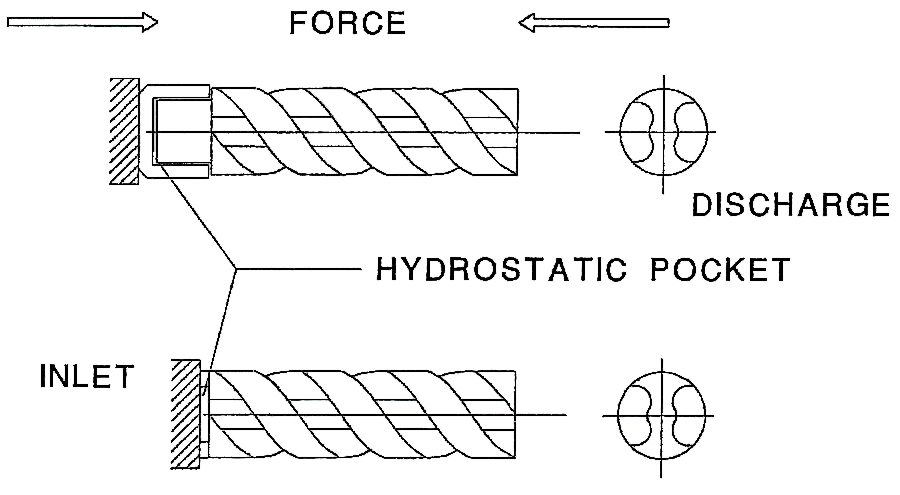
Axial and radial forces
In this section we’re looking into how the pressure affect the rotors in axial and radial directions. In addition to how to calculate the forces, we will also investigate how to balance the axial forces by static methods and more advanced dynamic balancing systems.
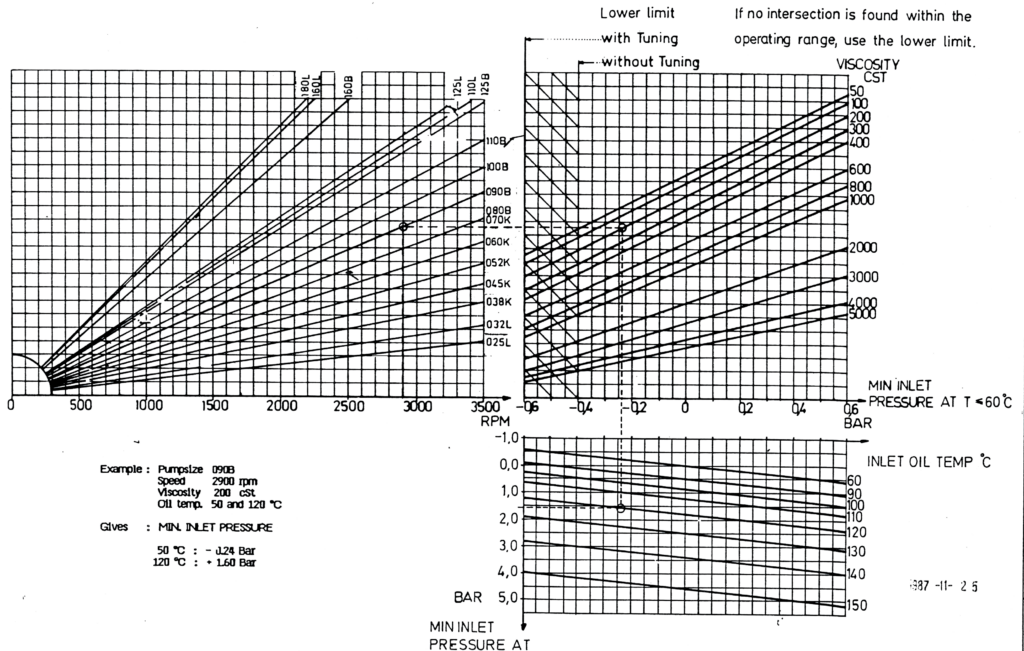
Performance
In this section we are discussing the basic performance quantities and how they can be calculated, such as flow, pressure, power, torque, efficiencies, cavitation, and start-up torque.
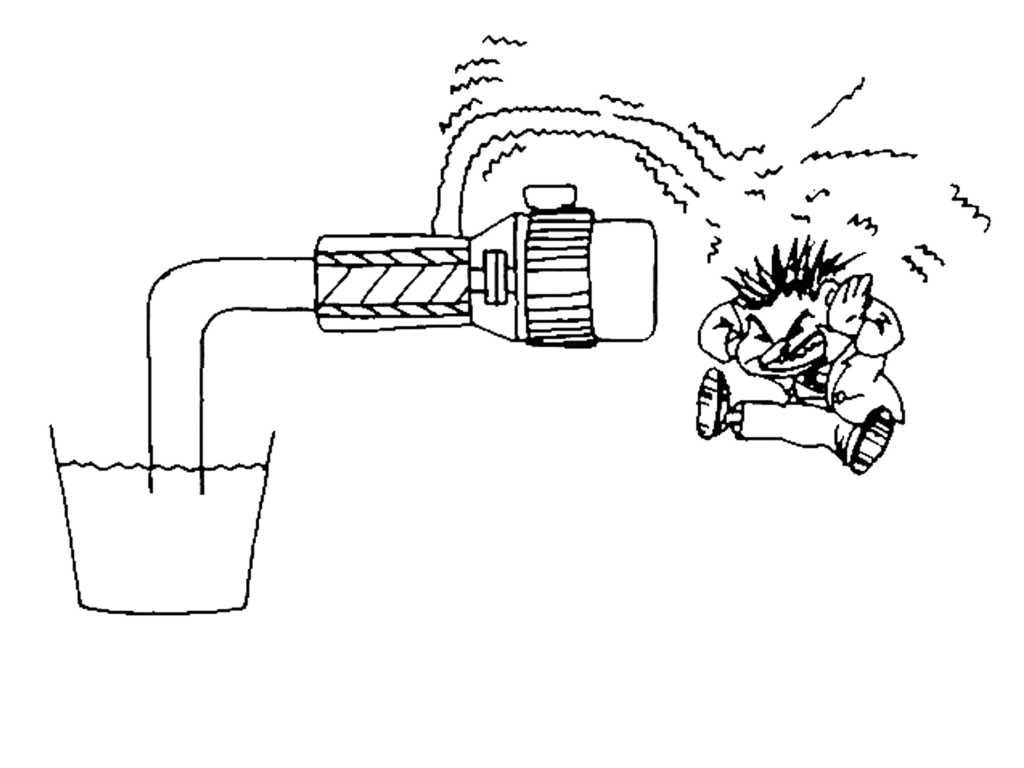
Cavitation
In this course section, we will explore the intricate details of calculating cavitation limits using Bernoulli’s equation. We will delve into the principles and methodologies required to determine the pump’s properties, specifically focusing on density and viscous flow losses. This will be achieved through the implementation of a sophisticated test program.
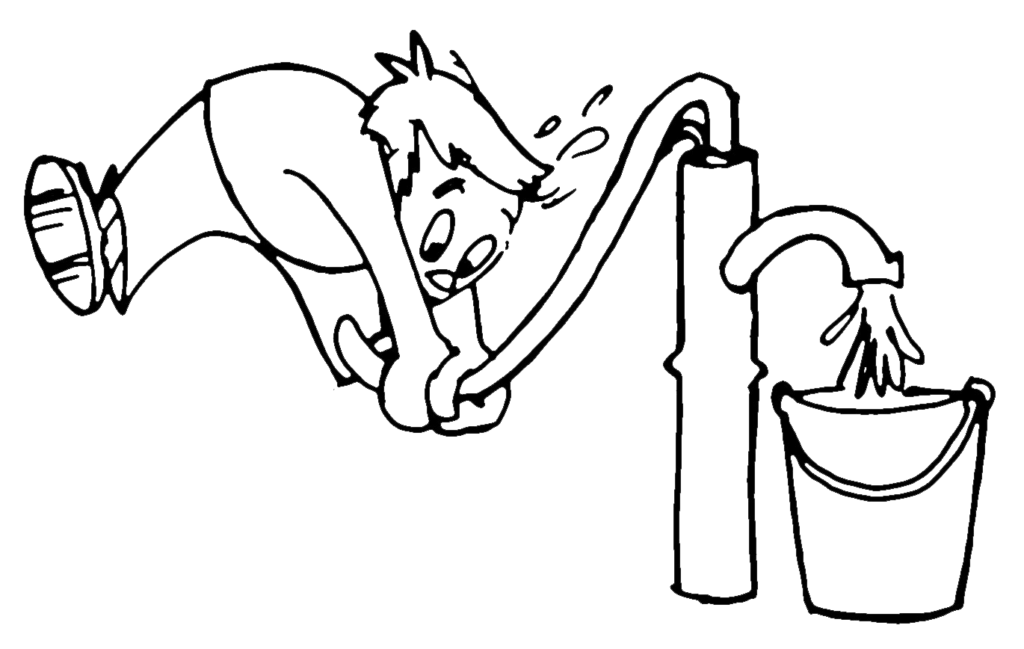
General pumps
This section is to get a basic understanding of pumps in general and specifically the three-screw pumps, we will also include pump systems. The target group is normally new employees or those who normally aren’t working close to the technology, but the level can of course be adjusted as needed.
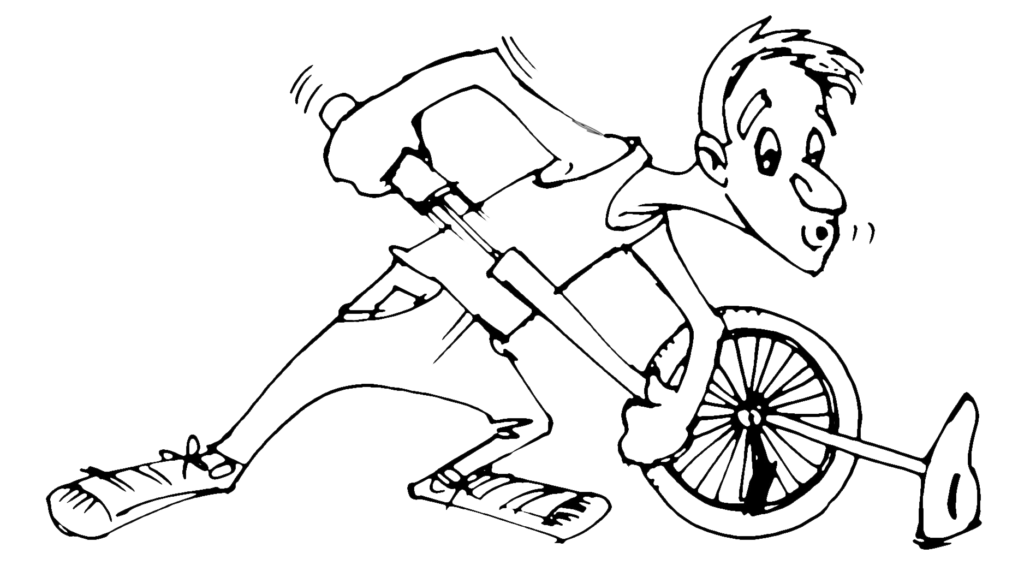
General compressor
This section is to get a basic understanding of compressors in general and specifically the screw compressor, we will also include compressor systems. The target group is normally new employees or those who normally aren’t working close to the technology, but the level can of course be adjusted as needed.
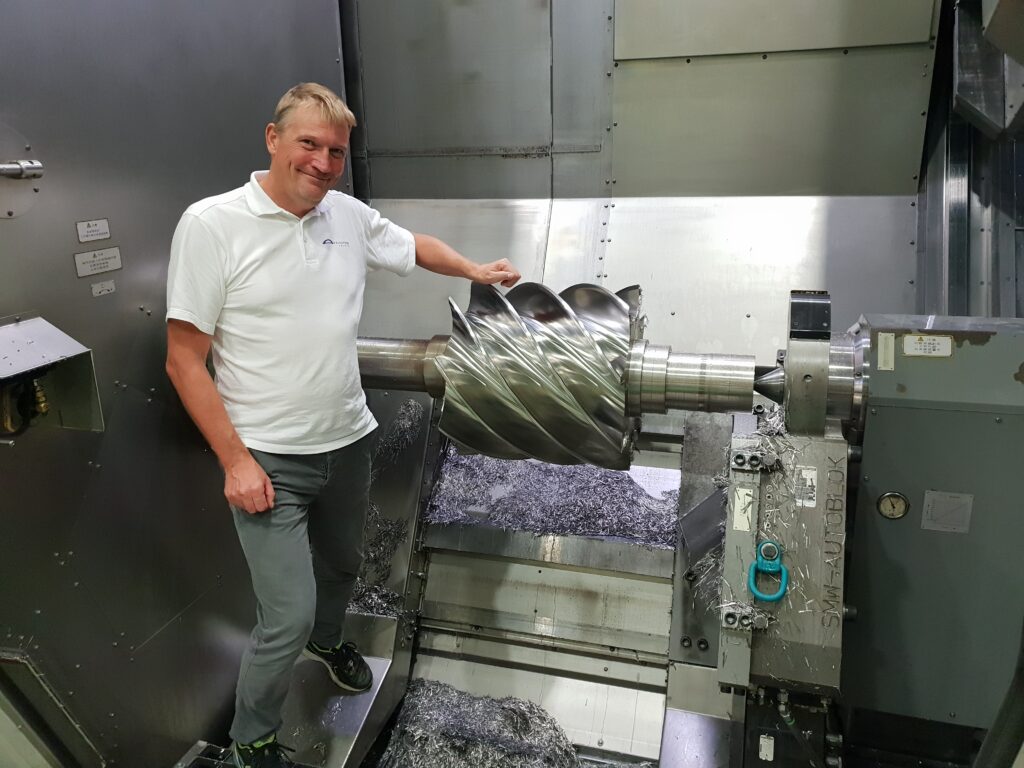
Rotor production
In this hands-on education section, we focus on discussing various rotor production methods and gaining a deeper understanding of the actual rotor production process at the company. We aim to explore the intricacies of rotor manufacturing and identify potential areas for improvement.